Preparing Your Plant For a New Machine
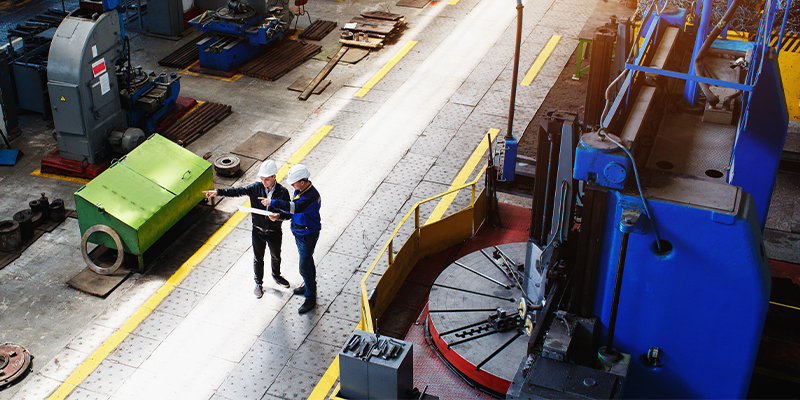
Top 5 Considerations When Preparing for a New Machine
When bringing a new machine into your plant or factory there are a couple things to consider and get in place prior to machine arrival to ensure a smoother installation.
1. Foundation
Does the foundation have enough mass and stiffness to support equilibrium?
The foundation needs to be capable of holding the applied load without settlement, flexing, or crushing. Typically this requires concrete or steel foundation when dealing with heavy machinery.
Some foundation options to consider are:
- Independent Concrete pad- The total foundation mass and any supportive structures should be AT LEAST 5 times the total rotating or moving mass of the machine-train. As a result, the concrete pad should be poured to account for enough mass and stiffness to properly support the machine-train. Additionally, consider general forces created by normal operations, and account for absorption on that front as well!
- Mounting on a mezzanine- Machines that don’t have enough of a support structure should be mounted to provide additional foundation support.
NOT RECOMMENDED
Direct mounting on concrete or deck plate floors- this approach introduces a resonance problem with machine forces being transmitted directly into the floor. This can result in higher than normal noise levels, or worse coincide with machine frequencies and create serious chronic problems.
2. Anchoring
Anchor bolts are a vital link between the machine and the foundation. They properly secure the machine to the floor and are a critical component of your installation process.
Some anchoring options to consider are:
- Bolt size: When considering bolt size look for bolts that ensure adequate holding torque and will prevent loosening over time.
- J-bolts- These are fixed into poured concrete and depend heavily on selecting the proper grade of bolt, as well as determining of the mounting pattern is rigid enough to lock the mounting plates to the foundation.
NOT RECOMMENDED
Hydraulic concrete and straight mounting bolts- these bolts tend to loosen over time.
3. Isolation
Heavy machines create a lot of excess energy. It can affect the quality of other machines in your factory if not properly addressed. Especially, if you multiple continuous process lines like paper machines, high-speed printing, and metal processing. This energy is called vibration and can either be absorbed by the foundation or trapped within the machine.
Some isolation options to consider are:
- Concrete pad independent from surrounding floor- When a machine is mounted on a concrete pad, this approach helps to absorb vibration generated internally, and also limits external vibration sources from affecting the machine.
- Springs or elastomeric pads- this approach is for when a machine must be mounted directly on the floor. Keep in mind that isolators are designed for specific, narrow bands of frequencies and will not isolate outside of those specs. Proper sizing and installation are key.
4. Leveling
Most machines are designed to operate on a horizontal plane. It’s important that once a machine is installed, the entire machine-train is level AND in the proper horizontal plane.
Some ways to measure level are:
- A liquid level- tried and true, this approach is typically sufficient when assessing whether your machine is level.
- Laser alignment device- new tech has introduced this approach, and it’s a faster more accurate option.
NOT RECOMMENDED
Using shim packs that do not provide full footprint support- the most common leveling failure is the method used to shim mounting feet. Shim packs provide a rigid connection between mounting feet and the foundation. The surfaces must be flat and parallel to ensure there are no voids or flexing in the final bolted joints.
5. Alignment
Proper alignment of the machine’s driver and driven units ensures that the common shaft between the outboard driver bearing and he driven unit are in the same vertical and horizontal planes.
Alignment tips:
- Measuring alignment- Reverse-dial indicators or laser alignment instruments are typically used to provide required alignment adjustments.
- Specs vary based on machine type- Typically, the shafts should be parallel and on the same plane within a maximum of 0.001 in to 0.002 in.
Are you or someone you know in the process of preparing for a new machine? Our experts can answer your questions and show you the best leveling and vibration options, we’re here to help!
{{cta(‘b8d1001a-9d83-407f-91d9-924b0e200dbd’,’center’)}}